- Categories
- Ringfeder: Shaft Coupling & Shaft Locking
- Locking Assemblies
- Ringfeder TNF Flange Couplings
- Ringfeder Elastomer Jaw Couplings TNB
- RINGFEDER TNR Torsional Highflex Couplings
- TSCHAN TNM Flexible Couplings
- Ringfeder TNS Jaw Couplings
- Ringfeder TNZ Gear Couplings
- Ringfeder TNK Barrel Coupling
- Ringfeder TNT Safety Couplings
- Ringfeder TND Torsionally Rigid Disc Couplings
- Ringfeder GWB Metal Bellows Couplings For Encoder
- Servo-insert Couplings GWE RIngfeder
- Servo-Insert Couplings
- Nylon Sleeve Gear Coupling ECT Ringfeder
- Ringfeder Friction Spring
- Ringfeder HENFEL: Hydrodynamic Coupling
- KTR: Shaft Coupling & Shaft Locking
- Cross-morse: Puly, taper bushes, shaft Coupling
- JAC coupling : Gear couplings & Jaw coupling
- PT Couplings: Shaft Couplings
- KBK: Shaft Couplings & Safety Couplings
- 8. Martin couplings and Martin Elastome Rings
- 9. Fenner: Fenner Coupling, Fenner Belt
- 10Wichmann: Universal Joint Shafts
- 11. ITALGIUNTI: Cardan Shaft Coupling
- 12. Westcar: Brake & Fluid couplings
- TRANSFLUID: Fluid Couplings
- 13. Backstop Ringspann Couplings
- Max Dynamic Couplings
- FLENDER: Shaft Couplings
- 16. STIEBER: Freewheel, Sprag Clutch, Backstop
- 17. Hilger u.Kern: Tester Devices
- Helmke: Electric motor AC Germany
- I.Mak: Gear Motors & Gear Units
- Ringfeder: Shaft Coupling & Shaft Locking
ONLINE SUPPORT

PRODUCTS
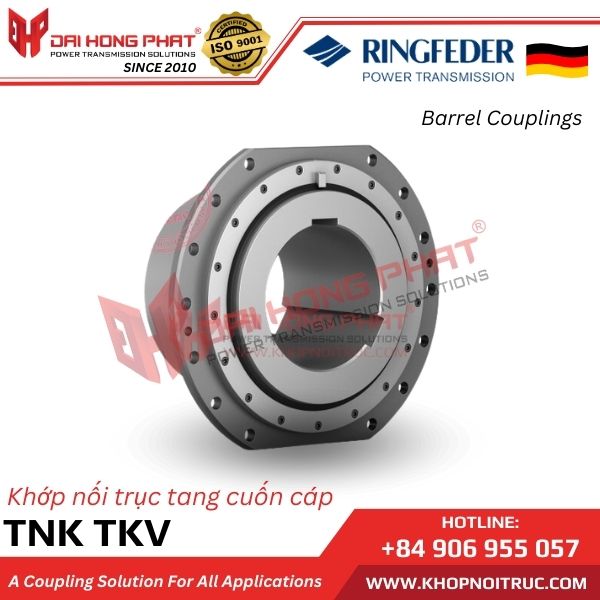
RINGFEDER TNK BARREL COUPLINGS TYPE TKV
DESCRIPTION: Ringfeder TNK ® TKV of reinforced-material Power improved design Proven design, hub and housing of reinforced material to transmit higher torque and higher radial load by same designed space
SPECIFICATIONS
Barrel Coupling Ringfeder TNK TKV Ringfeder
Ringfeder TNK TKV of reinforced-material
Power improved design
Proven design, hub and housing of reinforced material to transmit higher torque and higher radial load by same designed space
The RINGFEDER barrel coupling consists of a sleeve, made of reinforced-material, equipped with semi-circular internal teeth and a hub, made of reinforced-material, with semi-circular external teeth of the same shape. In the resulting circular recording hardened steel barrel rollers are used, which serve as power transmission elements. Lock rings on both sides of the barrel rollers serve for their axial guidance. Inner and outer covers, each of which is equipped with a lip seal, effectively prevent foreign matter from entering and lubricant from escaping.
The proven design with hub and housing made of high-strength material allows more torque and higher radial force in the same space.
RINGFEDER TNK serie TKV
Barrel couplings made of reinforced-material for use in crane/ hoist applications to support the rope drum.
Characteristics
Torsionally rigid, compensate for angular and axial shaft misalignment
Torque transmission by hardened, barrel shaped steel rollers
Equipped with wear indication
Outer diameters up to 850 mm
Bores up to 425 mm
Torques up to TKmax = 815,000 Nm
Maximal radial load Frad = 490,000 N
FEATURES AND APPLICATIONS Barrel Coupling Ringfeder TNK TKV Ringfeder
The barrel coupling consists of a sleeve, made of reinforced-material, equipped with semi-circular internal teeth and a hub, made of reinforced-material, with semi-circular external teeth of the same shape. In the resulting circular recording hardened steel barrel rollers are used, which serve as power transmission elements. Lock rings on both sides of the barrel rollers serve for their axial guidance. Inner and outer covers, each of which is equipped with a lip seal, effectively prevent foreign matter from entering and lubricant from escaping.
Due to the curved shape of the barrel rollers, it is possible to swing the hub relative to the housing, as a result of which angular alignment errors can be compensated. Depending on the size of the coupling, axial displacements of 3 mm to 8 mm can be accommodated during operation. The torque is transmitted by means of two carrier face on the housing and their counter-carrier face into the drum. The screws, used to connect the drum, support torque transmission.
By using high-strength materials for hub and sleeve, the transmission capability compared to the type TK could be significantly increased.
Barrel couplings are used in material handling technology and especially in crane hoists to connect rope drums to the gear output shaft with minimum axial space. In this application, the barrel coupling transmits high torques and large radial forces and yet acts as a joint. Thus, in a rigid connection of the gear shaft with a lifting drum a three-point bearing (Figure No. 1) and thus a statically indeterminate case would result.
Then a high alignment quality is required. However, unavoidable assembly inaccuracies, deflection of the foundation under load, and wear on the bearing cause enormous additional forces has to be absorbed by the stored gear shaft. Alternating bending stress can cause fatigue failure and bearing and gear damage.
In order to avoid this risk, barrel couplings between the gearbox and the rope drum are positioned, which, due to their characteristics, compensate angular misalignments. With the barrel coupling in a three-point bearings, a statically indeterminate becomes a statically determined drive train, whereby high bending moments and constraining forces are avoided. Figure 3 shows the assembly of a barrel coupling in a hoist. Taking into account that the coupling absorbs displacements and thus acts as a floating bearing, a spherical roller bearing is to be provided as a fixed bearing at the other end of the drum shaft.
Download catalogue Ringfeder TNK TKV
Size |
TKN [mm] |
d1 Max [mm] |
D [mm] |
C x nb7 x d [mm] |
L [mm] |
25 | 6500 | 66 | 250 | 220 - 10 - 15 | 95 |
50 | 8400 | 77 | 280 | 250 - 10 - 15 | 100 |
75 | 10500 | 88 | 320 | 280 - 10 - 19 | 110 |
100 | 16000 | 98 | 340 | 300 - 10 - 19 | 125 |
130 | 21500 | 112 | 360 | 320 - 10 - 19 | 130 |
160 | 27000 | 126 | 380 | 340 - 10 - 19 | 145 |
200 | 31500 | 140 | 400 | 360 - 10 -19 | 170 |
300 | 39000 | 155 | 420 | 380 - 10 - 19 | 175 |
400 | 53500 | 183 | 450 | 400 - 10 - 24 | 185 |
500 | 91000 | 210 | 510 | 460 - 10 - 24 | 220 |
600 | 127000 | 220 | 550 | 500 - 10 - 24 | 240 |
1000 | 180000 | 250 | 580 | 530 - 14 - 24 | 260 |
1500 | 241000 | 295 | 650 | 600 - 14 - 24 | 260 |
21000 | 360000 | 305 | 665 | 615 - 26 - 24 | 330 |
2600 | 425000 | 315 | 680 | 630 - 26 - 24 | 350 |
3400 | 529000 | 335 | 710 | 660 - 26 - -28 | 410 |
4200 | 660000 | 380 | 780 | 730 - 26 - 28 | 410 |
6200 | 815000 | 425 | 850 | 800 - 26 - 28 | 450 |